Elastomer seals are built to handle a wide range of demanding hydraulic and pneumatic applications. A seal’s design and its material properties are two keys to lasting performance, but experts also offer some important recommendations on proper safekeeping if seals will be stored for a period of time prior to installation.
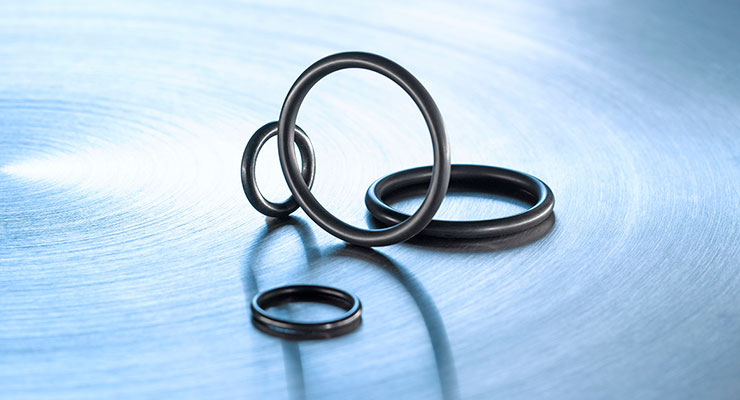
Elastomer properties typically remain constant for years if the seal is kept in a benign environment. Improper storage conditions, on the other hand, can drastically reduce a seal’s potential shelf life. To avoid this, many experts recommend following guidelines based on DIN 7716 and ISO 2230 standards for storage of elastomer seals. Suppliers and users of elastomer seals in the U.S., however, prefer to follow SAE AS5316 recommendations which are similar, but not the same, as the ISO standards.
As a bit of history, in 1998 the Society of Aerospace Engineers (SAE) issued Aerospace Recommended Practice 5316. ARP5316 became a leading protocol for determining the shelf life of aerospace elastomeric seals, as well as for industrial rubber seals, gaskets and commercial grade elastomers.
ARP5316 was actually cancelled in October 2018 and superseded by SAE AS5316 (“Storage of Elastomer Seals and Seal Assemblies”). While the two documents are much the same, the rationale, according to SAE International, is that there had been an industry need to convert to an Aerospace Standard because ARP5316 had been used as a standard even though it was a Recommended Practice.
For design engineers, a number of factors can influence seal storage. They are listed here based on ISO guidelines. The same criteria hold for AS5316, unless noted otherwise.
Temperature. The preferred storage temperature for elastomer products is 15°C (59°F) and should not exceed 25°C (77°F). Accordingly, avoid sources of heat such as radiators, boilers (minimum distance: 1 meter) or direct sunlight. Temperatures should not drop below -10°C (14°F). In this case elastomer products will stiffen, and seals should be handled with special care to prevent deformation. Chloroprene materials should not be stored below -12°C (10.4°F). AS5316 says storage temperature should be below 100°F (38°C).
Humidity. Ensure that the relative humidity in storage facilities is below 65%. Avoid humid rooms and condensation; likewise, elastomer seals should not be stored in extremely dry conditions. AS5316 recommends the relative humidity in storage shall be less than 75%, and less than 65% relative humidity for polyurethanes.
Light/radiation. Elastomer seals must be protected against sources of light with a high UV content that could damage the products. Examples include intense artificial light or direct sunlight. Avoid all types of radiation such as gamma or radioactive radiation.
Oxygen/ozone. Generally, elastomer seals should be protected against circulating air by suitable packaging such as airtight containers. This is particularly important for very small seals with a large surface-to-volume ratio. Mercury vapor lamps, fluorescent lights, electric motors — generally any device capable of producing ozone through sparks, electrical discharges or high-voltage fields — must be strictly avoided. This also applies to organic gases and combustion gases, as they are capable of producing ozone via photochemical processes.
Solvents/greases. Greases, oils and solvents may damage elastomer seals. Therefore, ensure that the seals cannot come into contact with these media in storage (unless packaged in this fashion by the manufacturer).
Deformation. Elastomer seals exposed to tensile or compressive stress or other types of deformation may result in damage or cracking. Therefore, seals must be stored without being subjected to strain, stretching (including hanging), twisting or compression.
Contact with dissimilar materials. Elastomeric seals should not come in contact with liquids like fuels, greases, disinfectants and cleaning fluids, or their vapors, at any time unless these materials are by design an integral part of the component or the manufacturer’s packaging. Likewise, avoid contact with metals (unless they are bonded together in a single unit.) Certain metals and alloys (in particular, copper, manganese, and iron) are known to damage elastomers. Finally, avoid contact between different elastomers and seals, and materials containing plasticizers, such as PVC.
Storage period. Shelf life is the storage period after manufacturing and before installation of elastomeric seals and seal assemblies into hardware components. Ideally, elastomer seals should be used within 24 months. Otherwise, the recommended maximum storage period depends on the type of elastomer.
Fluid-power engineers and users of elastomer seals should be aware that the DIN 7716 and ISO 2230 standards tend to be more stringent than the AS5316 guidelines often used in the U.S. Recommended maximum storage period per ISO and DIN guidelines for the following elastomers is:
- Polyurethane (TPU) and SBR: 5 years
- Hydrogenated nitrile (HNBR), nitrile (NBR) and chloroprene (CR): 7 years
- Ethylene propylene (EPDM), Fluorocarbon (FKM), silicone (VMQ), fluorosilicone (FVMQ), and perfluorelastomer (FFKM): 10 years
SAE AS5316 recommends a maximum storage period of:
- Polyurethane: 5 years.
- HNBR, NBR and CR: 15 years.
- EPDM, FKM, VMQ, FVMQ, and FFKM: “unlimited.”
Stored elastomer products should be inspected prior to installation. Negative changes due to improper storage can usually be detected by visual inspection. Discernable characteristics in a visual inspection are: permanent distortions, dirt deposits, surface damage, cracks, tears, hardening, softening, stickiness or discoloration. In such cases, the seal is no longer fit for use.
Following an inspection of these characteristics, the recommended maximum storage period may be extended. For small elastomer seals, due to the greater surface-to-volume ratio and the resulting risk of oxidative attack, the inspection cycle should be shortened.
Leave a Reply