Mining machines and equipment face tough and unforgiving operating conditions, and the hydraulic systems they rely on have to stand up to the abuse and, in some cases, extreme heat. Facing a unique combination of challenges, a mineral-processing OEM approached GS Global Resources, Mukwonago, Wisc., for engineering assistance while designing a massive 3,300-hp rock crusher, reportedly the largest open-pit cone crusher in the world.
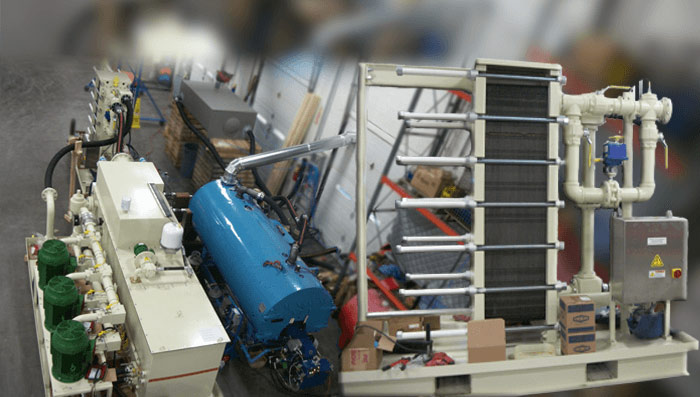
Hydraulic cone crushers feed raw material between two cone-shaped structures, one nested inside the other. Hydraulic actuators apply pressure to the two opposing cones, which rotate and stroke to efficiently pulverize rock and ensure high production rates.
Aside from its considerable size, the cone crusher would also be located in Zambia, posing multiple environmental issues including high ambient temperatures and an extremely caustic water supply. Due to the hot climate, large air coolers traditionally used in this application could not effectively remove heat from the oil.
That’s a problem for several reasons. Excessive heat reduces oil viscosity, which lowers the fluid’s ability to lubricate components and, in turn, induces surface wear and speeds failure. Heat also accelerates oxidation and breaks down additives which protect the entire system, and leads to the formation of sludge, varnish and other contaminants. High fluid system temperatures can also prematurely break down seals and other plastic components.
As an alternative method to reduce temperatures, this OEM would normally turn to shell-and-tube water coolers. However, to be fully effective, this application would require twelve 10-in. shell-and-tube heat exchangers, which would have led to an incredibly large footprint. GSGR was tasked with developing a different, more-efficient cooling method that could handle this unique set of environmental concerns.
The GSGR engineering team proposed installing flat-plate heat exchangers, a cooling technology that had yet to be used in the mining industry. Because this type of unit offers more flexibility than shell-and-tube systems in terms of the amount of heat that can be extracted, it could be adjusted to work in extremely hot climates. One issue, however, was the pH of the local water supply. As the water used in this application was so caustic that it would eat away at the stainless steel plates typically used in this type of heat exchanger, titanium plates were substituted, which were durable enough for the local water supply.
To test the new design, GSGR engineers developed a complex procedure to recreate the environmental constraints and operational issues. They simulated the heat load of the rock crusher and ran oil to the cooler. The flat-plate heat exchanger was supplied with water heated to 93° F, which was 8° higher than the hottest estimated temperatures in the machine’s environment. This elaborate test set-up let technicians monitor water and oil temperature changes across the cooler and guarantee that this cooling technology would perform well on site.
As a result, the OEM was able to launch the system in the field with confidence that it could work efficiently even in temperatures beyond what was required. The manufacturer embraced the newer, more durable and compact technology, and has since incorporated it into four additional machines.
GS Global Resources
www.gsglobalresources.com
Leave a Reply