By Josh Cosford, Contributing Editor
I once had a walk-in customer bring with him an old, rusty spin-on filter, which I believe was originally coloured white below the now orange and brown soup of rust and oil. He needed a replacement filter for his vacuum truck, a machine he said he bought used eight years ago. I grabbed a stock filter head to confirm thread and seal fitment, and casually asked him when the last time this filter was replaced. I was horrified when he responded with, “this is the first time.”
Maintenance means different things to different people. Just as some people visit the doctor only if and when they develop severe gout, when a daily maintenance plan of diet and exercise prevents the condition to begin with, so too did my customer practice reactive maintenance. I can’t help wondering how many other hydraulic components on that vacuum truck were ailing while its lifeblood was essentially circulating with no kidneys!
When it comes to maintaining your hydraulic machinery, you can subscribe to one of four plans; reactive, planned, preventive or predictive maintenance. The level in which you adhere to any of these tiers will directly and proportionately correspond to your machine uptime and productivity. Although each plan comes with an increasing commitment of time and money resources, so too does the equivalent payback.
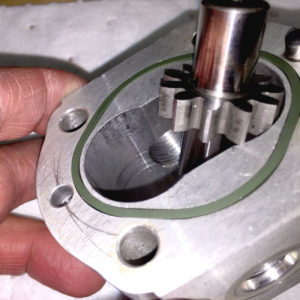
Reactive maintenance is the most stressful plan, although I should drop the word plan from the previous clause. A plan is a thoughtful collection of tasks for future completion, but reacting to your maintenance needs only when a component fails is not much of a plan. Reactive maintenance is more a result of a lazy and ignorant approach to machine care; generally not caring or knowing how and when to maintain your hydraulic machinery.
Reactive maintenance is far more common than anyone would like to admit, but the manufacturers of spare parts and the shops replacing those parts are glad their customers would prefer a $2,000 pump repair bill than the sale of a $100 filter element. Oil suppliers are happy you want to change out your 200 gallons of tank fluid rather than invest in a couple hundred dollars worth of desiccant breather caps per year. If you’re on the reactive maintenance plan at work, read on … you may want to upgrade.
Planned maintenance pays respect to the sensibilities of maintenance personnel, and ensures the hydraulic system gets regular attention … whether it needs it or not. The planned maintenance technique follows a calendar, and on regular days on typical months, the machine will have its filters changed, oil replaced or cylinders serviced. In many ways, planned maintenance is the superior way to keep the machine as close to new as possible.
The issue with planned maintenance is the exorbitant investment in time and money. Sure, your machine is “always new,” and rarely experiences breakdowns, but the cost to maintain can be higher than the cost of failures. Where absolute, no-option production uptime is the driving factor, planned maintenance is the way to go (think automotive). However, for the average user, the resources just aren’t there to justify it.
Although I’d love to have a new hydraulic machine every three months, it’s just not practical. Preventive maintenance is a method to maintain equipment as required just before components fail or are close to failure. For example, a machine operator may notice leakage from the D03 valve stack on their machine. Given time, the seal may blow out completely, leading to a catastrophic fluid loss. Upon recognition of the leakage, a “PM” can be planned for the machine, when the valve seals will be replaced during scheduled machine downtime.
Preventive maintenance sometimes involves replacing components based on known service life and hours of operation. For example, if a pump is known to provide 100,000 hours of service life, it could be replaced at the next scheduled PM as it approaches the end of its life. This method allows components to be replaced prior to failure, providing longer service life and lower cost than planned maintenance. However, unexpected failures still occur, and conversely, what if your pump could have lasted 150,000 hours?
Predictive maintenance tries to head failure off at the pass. By using tactics to predict when a maintenance event is required — and only when — you can save both time and money. For example, most hydraulic filter assemblies have a differential pressure port providing a reading of the back pressure being created as fluid flows over the filter element. As the filter becomes clogged, the backpressure rises as fluid finds it more difficult to sidestep the increasing number of particles. The pressure port can be fitted with a simple popup indictor, a pressure gauge or even an analog transducer. Each of these options allows you to compare backpressure to the bypass valve rating built into the filter. The bypass valve will open when pressure in the filter exceeds the valve’s rating, allowing fluid to flow freely (and unfiltered) to prevent collapse of the element.
By comparing the bypass valve pressure rating to the actual backpressure across the filter, you have datum to see how close the filter is to becoming clogged. As differential pressure approaches bypass pressure, then and only then do you replace the element. Predictive maintenance avoids the unnecessary cost and time of needless replacements, but also prevents failures related to neglected practice.
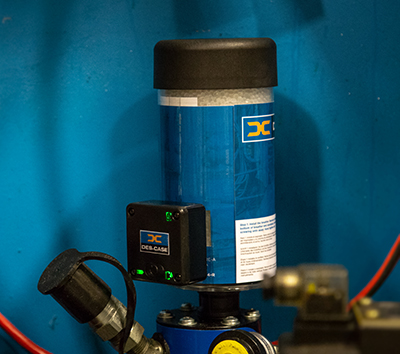
The Industrial Internet of Things, and the Industry 4.0 umbrella it falls under, are changing the way we maintain our machinery. What is being used on a plant floor today doesn’t always mirror what is potential with Industry 4.0, but the early concepts are promising. Imagine instead of changing a pump at 100,000 hours, you change it within a day of failure.
The technology already exists to monitor the temperature and flow of the pump’s case drain line, of which acceleration of flow and temperature occur as the pump wears. Adding vibration sensors to the pump’s bearings will fill you in if they’re about to blow. Now imagine if instead of dumb sensors, the case drain and bearings were monitored by Bluetooth enabled smart devices programmed to interpret its parameters and send a lifespan doomsday clock directly to your phone.
I could spend an entire article on predictive maintenance, especially with all the exponentially increasing technology flooding in with Industry 4.0. I want to be there the day the maintenance supervisor asks of his team member, “Hello, Aiden. I’m going to need you to go ahead and change that pump on Press 8M. It’s going to fail on Thursday morning, so if you could change it by Wednesday afternoon, that would be great.”
Leave a Reply