It’s critical for equipment manufacturers and the engineers they employ to possess a sound understanding of the composition of oils, the properties of lubricants, and how hydraulic fluids can impact machine performance.
With that fact in mind, IFPE 2020 will offer attendees an education session entitled “Hydraulic Fluid Properties, Efficiency and Contamination Control.” The Association of Equipment Manufacturers (AEM) recently spoke with the session’s presenter, Paul Michael, manager of Tribology Research at the Milwaukee School of Engineering (MSOE), to discuss hydraulic fluids, equipment, what attendees can expect him to share at IFPE 2020, and what key takeaways they’ll get from participating in his education session.
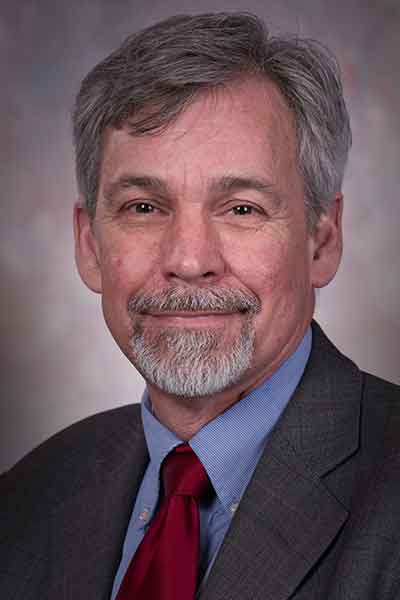
AEM: You are scheduled to speak at the upcoming IFPE 2020 show in Las Vegas, on the topic of hydraulic fluid properties, efficiency and contamination control. Can you briefly outline the topic and what attendees of your session can expect to learn?
Paul Michael: I think it’s important for both equipment manufacturers and end users to have a sound understanding of the fundamental principles by which hydraulic fluids function in a system.
There have been many upgrades in the quality of oils – in general – in the last two decades. Improvements in refining practices have led to the doubling of the life of oil. Oils are so much better now than before. Getting the maximum benefit out of a high-quality hydraulic fluid that has a great deal of longevity potential requires a good understanding of contamination control and filtration. It’s also necessary to understand the sources of contamination in hydraulic systems, as well as their impacts on a system.
Many of the more advanced hydraulic machines that are used in the industry these days have very sophisticated filtration systems to help keep the fluid clean throughout the life of the fluid. This is beneficial in that it provides the opportunity to extend oil change intervals through the use of oil analysis and other condition-monitoring technologies.
In my presentation at IFPE 2020, I’ll be talking about the fundamentals of hydraulic fluids, how they function, and their composition. I’ll discuss some of the more advanced technologies and fluids – synthetic fluids, fire-resistant hydraulic fluids and biodegradable fluids. After talking about the nature of the fluids, and how to validate their performance through standard testing, I’ll discuss contamination control, how to assess contamination level in terms of particle count, and present some case studies that look at the debris that’s found in the hydraulic oil filters, in order to identify the root cause of machine problems.
Some of the advanced technologies that will be discussed include the use of multi-grade hydraulic fluids and how advanced surface-active chemistries can improve the low-speed efficiency of hydraulic motors and reduce leakage flows throughout the hydraulic system, which is important for controlling energy usage and maximizing the productivity of the equipment.
AEM: Do you feel there are any notable misconceptions related to hydraulic fluids that are especially prevalent in the industry today?
Paul Michael: I think one of the biggest misconceptions out there right now is it’s a good idea to frequently change your oil. Often what happens when new oil is put into a hydraulic system, is that clean oil that has been circulated through a filter many times is replaced with marginal oil from a drum that has been filtered once at best. Several major original equipment manufacturers report that warranty claims spike after an oil change, so extending the oil change interval turns out to improve machine reliability.
AEM: Efficiency is always a point of emphasis for manufacturers as it relates to equipment today. However, when it comes to hydraulic fluid, what are some other ways in which equipment can be impacted?
Paul Michael: There are two measures of efficiency that apply. One is energy efficiency, which is basically the amount of energy required per work cycle. The other is productivity, which is the time required per work cycle. Fluids can affect energy consumption and productivity. In off-highway machines, productivity is generally the higher priority and fuel use is secondary. Since reliability impacts productivity, equipment users want equipment that is reliable, low-maintenance and, when maintenance is required, they want it to be predictable. Because — and it almost goes without saying — unplanned downtime is very expensive.
AEM: As technology continues to evolve with time, and the fluids that go into equipment changes, what will the industry need to keep front-of-mind in order to ensure machinery operates efficiently and effectively?
Paul Michael: There’s a trend towards using electrification in off-highway equipment and construction equipment to reduce emissions, noise and other concerns with heavy equipment. It turns out that the most expensive part of an electric machine is the battery. And in order to drive down the size and cost of the batteries used in those machines, you want to have the most efficient hydraulic system possible. Since the fluid can help maximize the hydraulic system efficiency, fluid optimization will play a role in driving future technology.
In most industries the value of clean hydraulic fluids is well recognized. And, as a result, modern hydraulic systems incorporate highly efficient filtration systems to purify the oil. It’s been repeated many, many times over and over again that 75% of all hydraulic system problems are caused by contamination in the fluid. My experience is that’s not accurate because of improvements in filtration practices. I would venture to say the No. 1 cause of “failures” in fluid power systems these days is leaks — leaky seals, leaky hoses, leaky fittings. Seal performance is an area that is getting more attention in our laboratory these days.
AEM: What knowledge do you want attendees of your session at IFPE 2020 to walk away with and be able to implement at their own companies?
Paul Michael: I would like attendees to come out of the presentation and become legitimate experts on fluid in their own organizations. My session covers a very broad landscape of hydraulic fluid properties, performance testing and maintenance requirements. And those in attendance can expect a very practical training program that provides a good understanding of the nature of the fluids, as well as how fluids impact system performance.
Learn More
Paul Michael, manager of Tribology Research at the Milwaukee School of Engineering, will conduct this education session entitled “Hydraulic Fluid Properties, Efficiency and Contamination Control” scheduled for Tuesday, March 10 from 8 a.m. to 12 p.m in West Gate Ballroom E-F.
IFPE
ifpe.com
Leave a Reply