There’s a growing realization that the type and formulation of hydraulic fluids can have a significant effect on machine efficiency, performance and overall life. But to date, fluid manufacturers have, for the most part, relied on traditional laboratory methods to develop new fluid chemistries.
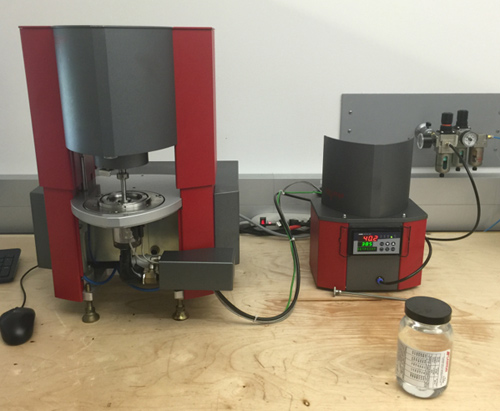
Now, in the project “Simulation, Rheology and Efficiency of Polymer Enhanced Fluids,” sponsored by the Center for Compact and Efficient Fluid Power, researchers will examine fluid behavior on the molecular scale. The research team led by Ashlie Martini, Professor of Mechanical Engineering at the University of California, Merced and Paul Michael, Research Chemist at the Milwaukee School of Engineering, looks to gain a better understanding of interactions on the atomic level. What they learn may ultimately lead to more-efficient hydraulic fluids.
“The high-level project goal is to find connections between the fundamental behavior of polymer-enhanced fluids and the performance of fluid-power systems,” said Martini. “Specifically, we’re trying to connect hydraulic efficiency to fluid rheology and then rheology to fluid molecular structure.”
A key tool in the research is molecular dynamics simulation, which can provide basic insights into material behavior and has not previously been applied to fluid-power applications.
Molecular dynamics simulation is a nanoscale modeling method, explained Martini. Empirical expressions describe the forces on atoms and molecules as they interact. The method starts with the initial configuration of the material to be modeled—in this case the basestock and additive molecules of a hydraulic fluid—and then the simulation predicts how that configuration changes over time.
“The empirical models are not new, but applying them to fluid-power systems is,” she said. “Our contribution is twofold. At the front end we model the molecules of interest—those of the fluid and the relevant additives.” Then the simulation runs and outputs the positions and forces on the atoms. “So we have to post-process the raw data to calculate fluid-power relevant properties like viscosity,” said Martini. In the end, researchers will link simulations with rheometer measurements and dynamometer testing of polymer-containing fluids.
The three-part project began in July and the first aim is to experimentally bridge rheology and efficiency. “Our first goal is to relate viscous properties measured in a rheometer to hydraulic efficiency. It’s certainly known that higher viscosity means less leakage, but we want to make those ties more quantitative and direct,” explained Martini.
Current work involves four ISO Grade 46 fluids with zinc (ZDDP) antiwear additives. Two are straight-grade fluids without polymer additives; and two are high-viscosity index multigrade fluids with two different polymethacrylate (PMA) additives. Rheometer tests confirmed that multigrade fluids have a higher viscosity at higher temperatures. Dynamometer testing of the fluids at Milwaukee School of Engineering showed that piston-pump flow losses were reduced by the higher-viscosity fluids, as expected, said Martini. Differences in the shear stability of fluids were also observed. After 200 hours of testing, the multigrade oils decreased in viscosity by 5 to 13% but the straight-grade oils were unchanged. While tests are ongoing and more data are needed, she said, the goal is to quantitatively correlate viscosity and shear stability to flow losses.
In the second part of the project, slated for this fall, molecular dynamics simulations of basestock with polymer additives will be used to model fluid properties, and rheological testing of viscous performance will validate those simulations.
The simulation studies involve fluids with polyisobutylene (PIB) polymer additives. There are several reasons for choosing PIBs, explained Martini, but most significantly, PIBs have simple and well-characterized molecular structures, so they’re amenable to molecular-dynamics modeling; they’re also smaller than PMAs and, thus, are more easily modeled; lastly, they can be purchased in relatively narrow molecular weight ranges, which makes them quite suitable for use in lab experiments.
The team is currently developing methods to study how concentration and polymer entanglement impact the viscosity of fluids with PIB additives. Molecular dynamics simulations will involve molecules of PAO 2 base fluid and PIB additives with different molecular weights and concentrations. “We want to explore how molecular weight and also entanglement of molecular chains affects viscous properties and rheology,” said Martini.
Researchers started by modeling the PIBs at two different molecular weights, combined them with models of the base fluid and adjusted system volume to ensure a 10% weight concentration. “In this way, we’ll be able to specifically isolate the effects of molecular weight and also the entanglement,” she said.
At the same time researchers will run rheology tests on actual PIB-containing fluids. Experiments using a cup-and-bob and parallel-plate rheometer will shear the fluid and generate a shear profile within the fluid. The ratio of shear strain and shear stress is the viscosity. “Effectively, the simulation does exactly the same thing: applying a shear strain, calculating the shear stress and the resulting ratio of the two will be the viscosity,” noted Martini.
Thus, they’ll actually measure the viscous behavior of the fluids and compare it to the simulations to determine the effect of molecular weight for a given concentration and also, how the PIB molecules interact or entangle to affect viscosity at different shear rates. From there, they’ll move on to different concentrations to introduce one more variable to the system.
Next spring, the researchers will link molecular simulations with the initial dynamometer studies. “We’ll introduce dynamometer testing and hope to relate efficiency to the viscosity and molecular features, and connect all three pieces of that puzzle,” said Martini. “As you can see, what we’re trying to do is pretty bold. We’re trying to go all the way from molecules to hydraulic efficiency, that’s a pretty big aggressive target.” But it will give a better understanding of the relationship between molecular structure and the behavior of fluids in hydraulic machines that may someday significantly benefit the fluid-power community.
University of California, Merced
www.ucmerced.edu
Milwaukee School of Engineering
www.msoe.edu
Center for Compact and Efficient Fluid Power
www.ccefp.org
Leave a Reply