Hydraulic development engineers and tribology specialists still expend substantial time, effort and resources in the search for an ideal hydraulic fluid. Novel Ionic Liquids may offer the solution.
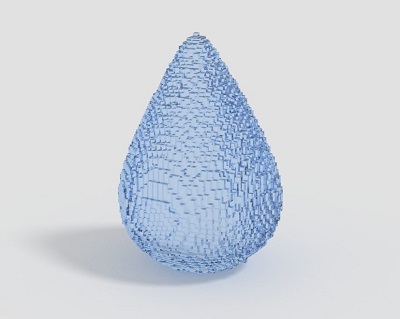
In a presentation at IFK 2020 titled “Basic aspects when using ionic liquids as a hydraulic fluid,” authors Darko Lovrec and Vito Tič of the University of Maribor, Slovenia, and Roland Kalb of Proionic GmbH, Grambach, Austria, gave an overview of the basic properties of Ionic Liquids and their suitability for use as hydraulic fluids.
The authors noted that a hydraulic fluid must fulfil many requirements: corrosion resistance, excellent lubricating properties, appropriate viscosity and compatibility with other materials, just to name a few. Lubricant manufacturers try to meet these requirements with special additives commonly added to mineral-based oil to improve certain properties, often at the expense of other properties. Ionic Liquids offer a completely new alternative that can reduce the shortcomings of typical oils.
IL basics
Ionic Liquids, a combination of cations and anions, are a new class of purely ionic, salt-like materials that are liquid at unusually low temperatures. They are recognized as promising high-performance lubricants and have attracted considerable attention within the field of tribology, although only a few studies have centered on IL use within hydraulic systems.
The choice of cation and anion, as well as the design of ion side chains, determine the fundamental properties of an IL. The number of possible combinations of anions and cations is extremely high (1018 combinations), which permits the creation of tailor-made fluids and additives to suit a particular use.
Lovrec said they are searching for “liquid salts” which would have the characteristics of a perfect hydraulic fluid. The authors tested several IL fluids against typical mineral oils as possible candidates for viable hydraulic fluids. Here are some preliminary conclusions.
Fluid properties
Corrosion resistance. Good corrosion protection is essential in a hydraulic fluid. Because Ionic Liquids are actually salts, one might expect that corrosion protection would not match that of conventional hydraulic mineral-based oils. That was, in part, confirmed by lab tests. In some ILs, corrosion protection was significantly worse compared to HLP mineral oil. Others, however, exhibited corrosion protection comparable to or better than standard oil, for both ferrous and copper-based non-ferrous metals in hydraulic components.
Lubrication properties. Lubrication properties were examined using a standard 4-ball test. The lubricating properties of ILs which passed the corrosion test were, in general, considerably better than those of conventional mineral-based hydraulic oils. The friction coefficient of mineral oil in a Stribeck test was considerably higher versus ILs.
Viscosity and density. Kinematic viscosity was measured by capillary viscometers at standard temperatures. The viscosity index values of higher refined mineral-based oils on the market are about 100 while multi-grade and synthetic oils have a VI around 150. The Ionic Liquids’ viscosity indexes are, in general, higher than those of HLP mineral oils. The viscosity of most ILs can be deliberately adjusted, which is a significant advantage of these liquids. The density of an IL hydraulic fluid is usually higher than that of mineral-based oils. This property is negatively reflected in areas like pressure loss and flow rate.
Compressibility. Bulk modulus of the fluid is crucial for hydraulic systems, particularly for high-pressure hydraulics where it can affect response and stability. ILs are less compressible than conventional mineral oils (low bulk modulus) and even water-based fluids. This makes ILs extremely interesting for hydraulic applications.
Electric breakdown voltage. In some cases, hydraulic fluids must have good electric insulation properties, for example when an electric motor is submerged in hydraulic fluid. The breakdown voltages of mineral oils are very high and are quite comparable with the best transformer oils (usually 40 to 60 kV). On the other hand, the breakdown voltages of most ILs are low. Therefore, they are not suitable for applications where an electric motor is submerged in oil.
Filterability. The ability of hydraulic fluid to flow through fine filter elements without clogging was analyzed according to ISO 13357 Standard, which uses a cellulose filter. In these tests, the ILs were not compatible with cellulose membrane filters. The filter membranes deformed and, in one case, the cellulose element started to decompose immediately after contact with liquid and dissolved rapidly. So determination of filterability by this method was not possible. However, in practice, there were no significant problems with IL compatibility when other filter materials were used.
Material compatibility
Paint. Most hydraulic tanks are painted inside and out. Immersion tests showed that IL fluids readily attacked epoxy-paint coated samples. The paint coat started to wrinkle and peel off where the plate was permanently submerged into the test liquid.
Seal compatibility. The compatibility of an elastomer with hydraulic fluid is a critical factor in system performance. There are numerous elastomer seal materials, with nitrile (NBR), fluorocarbon (FKM), ethylene propylene (EPR, EPDM), chloroprene (CR), and urethane (AU, EU) among the most common for industrial applications.
Seal compatibility tests were performed according to ASTM D1414. Tests performed on O-rings examined hardness change, volume swell and shrinkage, as well as mechanical attributes like tensile strength and elongation changes.
After conducting compatibility tests of most common sealing materials with certain types of ILs, we came to interesting findings. In some cases, no changes in dimensions, mass and volume of O-ring were observed, as well as no change in color of the seal (for example, POM and PTFE) or only minor changes (NBR, EPDM, MVQ). On the other hand, some sealing materials in combination with certain ILs completely decomposed in a short time.
In addition, the most suitable sealing material for a given IL (according to the standard test) turned out to be less suitable during actual operation, while a less-appropriate test sample actually worked better.
This does not directly provide useful guidance on the selection of suitable sealing materials with a specific type of IL but, rather, shows how extremely complex it is to test otherwise well-known materials with new types of fluids. Furthermore, test results obtained by standardized tests may not be directly applicable to real-life operating conditions.
These limited results show that some IL hydraulics fluids offer better properties than mineral oil. But, on the other hand, they are not compatible with paint and can’t use cellulose filter elements. At present, one of the greatest limitations for wider use of Ionic Liquids in hydraulic systems is a considerably higher price, compared to conventional hydraulic mineral oil — due to production in only small quantities.
The target applications of Ionic Liquids in hydraulic equipment are currently small-volume hydraulic systems, such as found in wind turbines and mobile hydraulic equipment. It follows that each type of IL needs to be tested individually for each important property, although some of its properties have proven to be excellent. The information can serve as a guideline for the selection and use of IL hydraulic fluid, as well as for the development of future Ionic Liquids.
Proionic
proionic.com
University of Maribor
www.um.si
Leave a Reply