Filter carts are mobile kidney loop systems that contain a motor, a pump and a filter to form an independent unit. Filter carts can generally be used in two different ways: as enhancement to existing hydraulic system filters, and as fluid preparation for use in hydraulic systems after an event (e.g. replacing fluid, repairs, maintenance, etc.). Dan Zoller, Group Product Manager Filter Systems, at Schroeder Industries says that in addition, filter carts can be equipped with contamination sensors to measure fluid cleanliness directly for displaying values, data collection or for controlling function (e.g. stop the filter cart after target cleanliness has been reached).
Filter carts with dual filters, often called staged filtration, are preferred. “This allows removal of larger particles in the first filter and smaller particles in the second filter. E.g. a 10 Micron element in the first filter and a 5 Micron element in the second filter prevents the first filter from filling-up prematurely and allow element change intervals to be aligned more closely on both filters. In addition, the first filter can be equipped with a water absorbing element to remove free water, if the fluid has high water content.” Zoller said.
Enhancement of hydraulic system fluid filtration
Zoller noted that hydraulic systems are generally equipped with system filters that are either placed on the pressure side (e.g. downstream of pumps, before system components) or on the return side (e.g. before fluid is reaching the reservoir). “However, in a case where only one filter is used, this one filter has to remove all the dirt generate in the system,” he said. “By using two filters in the system (e.g. pressure and return filters) the work load is shared and it is easier to maintain a fluid cleanliness level recommended for the hydraulic system.”
“Even so, the reservoir might still contain contamination accumulated over time and from the environment. This is where a filter cart answers the need. In order to improve the reservoir cleanliness and to help in extending the life expectancy of the elements in the system filters, a filter cart can be applied to the reservoir.”
Another example for the use of a filter cart is for regular cleaning of the gear box fluid with a high viscosity filter cart.
“This will remove particulate contamination, and free water with use of an absorbing element. This results in the extended life expectancy of the bearings and gears of the gear box and preventing costly repairs and unscheduled down times.”
Fluid/System preparation before start-up
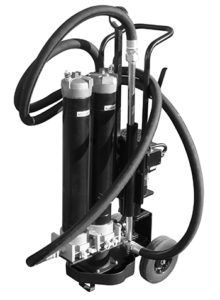
“It is a general misconception that new oil means clean oil,” Zoller warned. “The fluid delivered varies in cleanliness depending on the method of delivery. In any case, new fluid should be cleaned (filtered) before use to achieve a suitable cleanliness for modern, high pressure hydraulic systems. A filter cart can be used to kidney loop the fluid in the drum or tote and to finally move the fluid to the reservoir as well.”
He added that as a general rule, fluid that is moved (e.g. transferring fluid from storage tanks and drums to system reservoirs) should always be filtered. The fluid cleanliness level in the reservoir should be 1 to 2 ISO Codes below the required Target Cleanliness level in the hydraulic system.
The overall contamination level of a hydraulic system being built in an assembly plant is generally high. The overall contamination (particulates) consists of contamination that already exists in the new fluid, contamination that is already on/in supplied components and contamination introduced during the build process form the surroundings. The sum of all the contamination can be considered the Initial Contamination Level.
“The objective is to reduce this Initial Contamination Level,” he said. “The investment in time and equipment is worthwhile because of a reduction of costly warranty claims and for quality control and tracing purposes of products.”
“Incoming warranty claims can be investigated and connected to maintenance activities at the customer location. If the fluid was not maintained to recommended cleanliness standards during use, e.g. what was achieved when the equipment left manufacturing, a warranty claim could be rejected. Overall, manufacturers have found that clean hydraulic systems will reduce the occurrence of failure during the warranty period. A Filter Cart can accomplished the flushing of the system before delivery to the customer.”
Zoller said that it is simply a given that all hydraulic systems need maintenance, repairs, overalls, and upgrades over time. “This is even more important when a system is working with higher pressure levels and at a faster pace than in the past.”
“It is important to remember that working on any hydraulic system will introduce dirt in to the system and reservoir that must be removed before the system is started up. Any dirt left can cause the system or components to fail again resulting in additional costly downtime and repairs. It is important to assure that a good fluid flow through the reservoir is achieved and no pockets of dirt are left behind. Those pockets of dirt can mix with the clean fluid after start-up and could cause problems in the process. A filter cart is the ideal method to clean the fluid before the start-up, and whenever needed to keep all hydraulic systems in top shape.”
By Joyce Laird
Leave a Reply