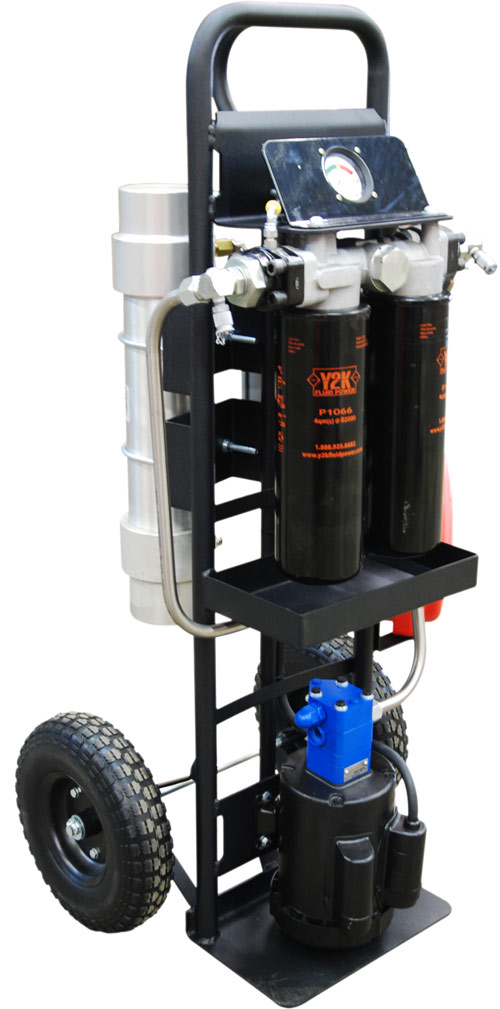
Most fluid-power users understand that particulate contamination in hydraulic oil can markedly degrade the performance and life of mobile and industrial machinery. Perhaps less recognized is that water contamination in the oil can similarly lead to component failure.
Water, whether dissolved in the oil, present in an emulsion or as free water, is harmful. It can reduce the lubricating capacity of the fluid, attack metallic surfaces, accelerate aging of the base oil, degrade additives, and help form sludge and sediment. Thus, it’s essential to control moisture in hydraulic systems to ensure top performance.
A number of manufacturers offer contamination-control designs that can help prevent water problems in a circuit. When users need to remove large amounts of water from reservoirs, but lack the portability and electrical requirements of conventional vacuum dehydration systems, Y2K Fluid Power, Sioux Falls, S.D., has developed a portable unit to address that need.
Its Membrane Dehydration System fits on a standard filter-cart frame, making it easy to transport and move through doors, catwalks and most hard-to-reach areas where a conventional dryer cannot fit, according to the company.
It works based on advanced membrane-separation technology where water passes directly from the oil into a dry air (or vacuum) stream. The engineered membranes let only certain-size molecules (water) pass through the material for collection and removal, while larger molecules (hydrocarbons) remain inside.
In operation, oil flows over a patented structured packing in the membrane separator which distributes oil into relatively thin films with a large contact area. Dry compressed air is used to create a driving force for mass transfer of the water from the oil, through the membrane, and into the air. Air containing water vapor then exhausts to atmosphere. This system avoids the problems usually associated with conventional vacuum purifiers, such as foaming, flooding and viscosity changes.
To ensure the incoming compressed air is clean and dry, a coalescing prefilter first traps dirt and oil from the plant air. Then, the humid flow enters a membrane air dryer, consisting of a small vessel filled with a bundle of hollow, membrane tubes. The volume outside the tubes but inside the vessel itself is at atmospheric pressure, creating a pressure differential across the tube walls. Inlet air passes through the tubes and the pressure differential lets only water molecules pass through the membrane, and dry air exits the unit. A small amount of dry, purged air recirculates outside the tubes and carries the water vapor away. Dried air exits with a dew point as low as -40° F for subsequent use in the oil-drying section.
The portable dehydrator handles oil viscosities up to 600 cSt (ISO VG 680) at 100° F with ambient temperatures ranging from –15° to 180° F. It removes 100% of free water, 100% of emulsified water and dissolved water to ≤25 ppm. Typically, the degree of water removal depends on the type of oil, its affinity for water (water solubility) and the rate of water ingression into the system.
The unit also filters particulates to ≤3 µm in size. Replacement filter elements come in a range of ratings, from β4(c) = 2000 (ISO Code 14/12/9—13/11/8) to β25(c) = 2000 (ISO Code 20/18/15—19/17/14). Slide-bar filter indicators trigger at 50 psid to signal the need for an element change.
The carbon-steel cart includes a 1-hp, 115 Vac/60 Hz motor and a heavy-duty steel gear pump available in 2 and 5 gpm versions. Two 7-ft long suction and discharge hoses made of clear, steel-reinforced PVC come with a variety of quick-connect couplings. Options include a moisture-monitor system and an onboard air compressor, and the unit is customizable upon request.
The dryers are used across a wide range of industries, including automotive manufacturing, steel making, paper production, power generation and mining. Typical applications include contamination control in hydraulic reservoirs, pulp and paper lube systems and gearboxes, and cooling tower gearboxes.
Y2K Fluid Power
y2kfluidpower.com
Leave a Reply