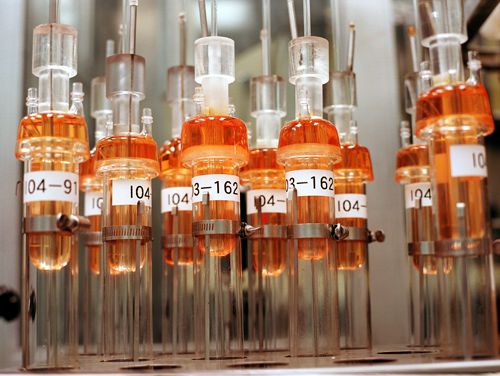
In recent years, operating pressure and power density in many newer hydraulic systems have increased significantly. Not too long ago, pressures in circuits topped out at around 3,000 psi. Now, systems running at 5,000 to 7,000 psi or more aren’t uncommon. On one hand, that can mean better performance, smaller and lighter components and, possibly, sizeable cost savings. On the other, it can also increase the susceptibility to wear and premature failures in hydraulic systems.
New-generation pumps and motors are designed to handle higher loads and offer long life. However, one can’t always say the same for the fluids they use. That’s because the type and quality of oil has a significant impact on the wear characteristics of hydraulic components and, with it, the reliability and longevity of fluid-power systems.
Unfortunately, as hydraulic components and systems have rapidly evolved to meet more-rigorous operating conditions, the standards for rating fluids have not kept pace. According to engineers at Bosch Rexroth, the problem is that while pressures, temperatures and oil-circulation rates have risen sharply, the minimum requirements of relevant standards like ISO 15380 and ISO 12922 do not reflect the elevated loads and stresses that today’s hydraulic fluids face.
One result is that a high-pressure circuit may run trouble-free with one fluid but quickly fail with another—even though both fluids meet the same standard.
Until now, machine manufacturers could only rely on arduous and expensive trial-and-error tests to find suitable fluids that meet their application requirements. To address that, Bosch Rexroth recently developed a new evaluation method for rating hydraulic fluids that realistically reflects higher performance demands.
In the test, described in Rexroth data sheet RDE 90235, technicians assess the behavior of fluids and their interactions with components like axial-piston pumps and motors in hydrostatic drives, under real-life conditions.
The Bosch Rexroth test goes far beyond current DIN and ISO requirements, explained a spokesman for German fluids manufacturer Liqui Moly. “Conventional tests work with 350 bar; the new standard up to 500 bar,” he said. And the Rexroth rating has an oil stress factor 13 times more severe than seen in the Eaton 35VQ25 pump test, which is widely recognized as a typical mainstream hydraulic-fluid qualification, according to engineers at Shell Oil.
Rating criteria are based on component weight and dimensional changes, material compatibility issues, and the degree of fluid breakdown during the tests. From this, technicians report conclusions on the long-term running behavior of the components based on how well the test fluid stands up. Currently worldwide, only products from four oil and lubricant manufacturers: Fuchs, Liqui Moly, Shell and SRS, meet all the requirements and make the list.
The upshot, according to the suppliers, is that these approved high-performance fluids offer a host of benefits for machine builders and users. Not only can equipment run with higher loads and temperatures, components see less wear and last longer, reservoirs and lines can be smaller, and fluid change intervals are longer—all which leads to less downtime and lower costs, versus machines running on conventional hydraulic oils. Look for more companies to get on the approval list soon, or for OEMs to reconsider their fluids suppliers.
Leave a Reply