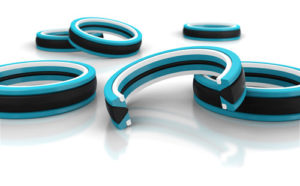
Sealing expert Joe Woods, Fluid Power Segment Manager Americas for Trelleborg Sealing Solutions, recently visited the offices of Fluid Power World and WTWH Media. We discussed some timely topics concerning the sealing aspects of the fluid-power industry, and on new developments at Trelleborg. Here are some takeaways.
Current business climate
Woods has been in the sealing business with Trelleborg for more than 20 years, and in his eyes there’s a noticeable concern about the cylinder segment of the business. “It’s a very mature marketplace, and it may be headed toward a slow down,” he said. It stems from a lack of change from a technology standpoint among some domestic manufacturers, he explained. As a group, they tend to purchase components from the same group of suppliers while relying on manufacturing processes that have remained relatively unchanged over the years. There hasn’t been any real paradigm shift in the way of doing business.
As a result of this business model, there are now foreign competitors establishing a very strong presence within the Americas. “Ten years ago everyone dismissed this possibility, now it’s coming to fruition,” said Wood. “If the industry doesn’t start to change, then they’ll wonder where all the business went,” he said.
Possible solutions
There are many seal manufacturers—large and small—in operation around the globe. But one can count the number of producers of highly engineered sealing systems on one hand, said Woods. These few companies, such as Trelleborg, are well staffed with experienced product specialists and design and application engineers, and these companies invest heavily on R&D in areas like materials development and tribology. When a cylinder manufacturer or OEM needs a solution or help with a next-level design, these are the go-to guys.
For cylinder producers to survive and prosper, they need to embrace state-of-the-art engineering and manufacturing of their products, and that includes the sealing systems. Some traditional manufacturers have sought out Trelleborg’s expertise, with outstanding results. Woods cited one recent “win” that moved a company away from the status quo. In this case, Trelleborg’s engineers helped them revamp their products, install a leaner method of producing cylinders and provide ongoing support. The result has been a significant gain in market share for the OEM. Not surprisingly, a number of other cylinder producers have taken notice of the shift, and have approached Trelleborg to learn how they can do the same.
It’s helping jump-start the industry, noted Woods. And it’s very good for Trelleborg, too. “It’s creating greater brand awareness and pushing our technology to the forefront. And it’s creating a momentum in what might be considered a stagnant marketplace,” he said.
New solutions
Trelleborg is also investing in new solutions and services that will improve the performance and efficiency of fluid-power systems and machines. One of the newer solutions is called “Lubrication Management.” According to Woods, it’s based on a new sealing concept where the system adjusts the seal profile for higher pressures, lower friction, less heat and longer life. In essence, it manages the fluid film under the seal, depending on operating conditions.
According to the company’s web site, the new development balances the conflicting trade-offs of maximum sealing effect, minimum friction and lowest possible wear in sealing systems. Lubrication Management regulates the seal system’s lubrication film to match the load on the individual elements. And it produces benefits exactly where the impact on the tribological conditions is greatest—in the sealing gap, the contact area between the seal and mating surface. Lubrication Management better lubricates the primary seal and provides an optimized lubricating film for the secondary seal. As a result, the load of the entire sealing system decreases even if the application’s operating demands increase.
While it is fundamentally a pressure-energized lip seal, said Woods, it combines several sealing elements that result in a new technique that better manages fluid leakage as pressures get increasingly higher. It will be of interest to any of the large OEMs, such as construction and off-highway equipment manufacturers, as well as many other users of hydraulic cylinders. Expect to hear more about it at IFPE in early 2017, he added.
Trelleborg Sealing Solutions
tss.trelleborg.com
Leave a Reply